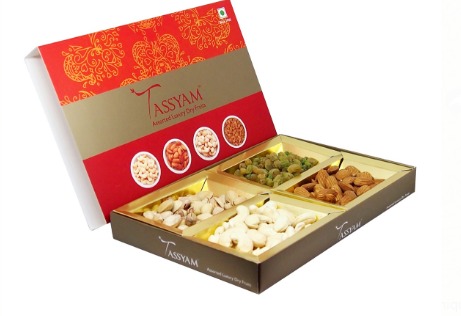
Due to its numerous advantages, additive manufacturing has become a current trend in manufacturing processes. It is defined as the layer-by-layer deposition of material for the purpose of manufacturing components. Many researchers have studied and reviewed it extensively. A detailed overview of additive manufacturing has been completed in this paper. The different phases of additive manufacturing’s growth as a significant technology are explored. The significance of part orientation, calculation of build time, and cost computation has also been discussed. The identification of issues connected with various additive manufacturing processes is a noteworthy element of this work. Because additive manufacturing has flaws, it has been urged that it be combined with other technologies, such as subtractive manufacturing. Innovative and cutting-edge research efforts connected with manufacturing processes, materials,
and product design are critical to the growth of industries. In addition to the traditional expectations
for cheap prices and high quality, market competitiveness in today’s manufacturing sectors is
connected to demands for goods that are complex, have shorter life cycles, have faster delivery
times, require customisation, and require less trained people. In reality, the present generation of items is extremely difficult to develop. As a result, there is a tremendous motivation to create, develop, and deploy new and innovative manufacturing methods.In the 1980s, Kodama released an essay titled “Three-Dimensional Data Display by Automatic Preparation of a Three-Dimensional Model,” which was the first to show AM. 2 In 1987, Chuck Hull (courtesy of 3D Systems) invented STL, a process that uses a laser to solidify small layers of ultraviolet (UV) light-sensitive liquid polymer. With fewer trained employees, quicker delivery times, and shorter product life cycles, it can effectively create complicated and customized goods. Figure 3 depicts an increase in the number of patents connected with AM between 1982 and 2012. It can be seen that AM technology began to emerge in the 1980s for the purpose of creating 3D things from CAD files. Every year after then, as indicated in Figure 3, either a new AM principle was invented or a current one was improved. It may be argued that in the future, Industry 4.0, AM will undoubtedly change and revolutionize production. The need for AM has shifted from automobiles and airplanes to micron-sized particles that may be used in the manufacturing of tiny devices and batteries. There’s even a 3D printer (courtesy of Photonic Professional GT) on the market that can make parts as small as human hair. Additive manufacturing is a disruptive technology that is predicted to transform manufacturing technology and have a worldwide impact on value chains. Polymers, metals, ceramics, and composites are among the materials that are available. In light of selected applications and production scenarios, the keynote will provide an overview of available manufacturing processes for various material groups and discuss the specific advantages of additive manufacturing – for example, the realization of complex geometries, part count and assembly effort reduction, part-to-part approach. The promise of additive manufacturing (AM) has always been enormous, but it has been hampered by unattractive economics, material and production restrictions, and an inability to scale,” according to the firm. “The newest 3D/AM printing platform advancements, including hardware, software, and materials, are combining to enable firms to create in new ways – while erasing all previous restrictions. The transition is already taking place: according to a recent study commissioned by Essentium, two- thirds of firms have more than quadrupled their usage of industrial-scale AM in the last year.The expanding diversity of materials processed by AM techniques was covered in the previous section, but the focus was mostly on known compositions transferred from conventional to the wide range of AM production processes. In recent years, significant progress has been achieved in alloy creation specifically geared for AM techniques like powder-based LBM, utilizing the laser’s severe intrinsic thermal conditions, notably fast melt pool solidification and platform temperature control for in-situ heat treatment. Advanced aluminum alloys with improved characteristics, in addition to innovative steel grades.